Glass Reinforced Plastic (GRP) is a versatile, sustainable construction material. It offers a range of key environmental benefits and is often used in place of traditional materials such as steel or aluminium.
GRP is a combination of structural glass fiber mats and synthetic resin, usually an epoxy, vinylester or polyester thermosetting resin. The resin provides the environmental and chemical resistance, while the glass fibers provide strength. Discover more items at grp cabinets.
Sustainability
Glass Reinforced Plastic (GRP) also referred to as fibreglass, composite plastic or FRP is a strong and lightweight material that can be used across a wide range of industries. Its innate qualities make it highly versatile and it is becoming increasingly recognised for the significant contribution it can offer to sustainable construction.
GRP is much more environmentally friendly than many people realise. It consumes very little energy compared to its natural counterparts, even after processing and machining. The production of GRP uses around 75% less energy than steel and the curing process is exothermic, using only a small amount of energy.
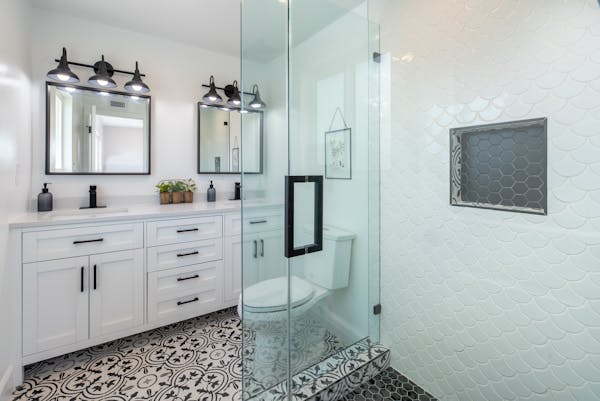
GRP pipework is particularly beneficial to the environment because it does not corrode in acidic soils. This is a huge improvement on concrete or metal pipes, which damage the ground by leaching chemicals into it. The resulting erosion can cause a number of problems including contaminated water supplies and lowered soil bearing capacity.
Durability
GRP is a versatile material that has a wide range of applications and offers benefits that align with sustainability goals and eco-consciousness. This includes low thermal conductivity and corrosion resistance.
Glass fiber-reinforced plastic (GRP) is a combination of glass fibres and either a thermoset or thermoplastic polymer matrix. The glass fibres may be randomly arranged, flattened into a chopped strand mat or woven into a glass cloth and then impregnated with a synthetic resin such as polyester or epoxy. The result is a strong, durable and lightweight composite that can be moulded into various shapes and used in a variety of industries.
GRP components are often adhesively bonded to substrates such as metal, concrete and timber. To prevent premature bond failure, it’s important that GRP sheets and components are heat-treated for a few hours to stabilise them – this is known as tempering. Untempered components may experience continual shrinkage that can lead to stresses on adhesive bonds and other surface defects, which could damage the overall structure.
Lightweight
GRP (also known as FRP or fibreglass) is strong, lightweight and highly versatile. It behaves differently to conventional thermoplastics found in many everyday items and is used across many industries for a variety of purposes.
The most commonly used reinforcement material is glass fibre but carbon or aramid is also utilised. This is combined with an epoxy, vinyl ester or polyester thermosetting plastic resin to produce GRP.
Fibre mats are web-form reinforcing materials woven with chopped or continuous glass fibres. Chopped fibres are used in processes where short 0.2-0.3 mm strands of glass are required, whereas continuous fibres are used for woven mats and fabrics where high strength and stiffness are desired.
This combination is then moulded into the required section shape using process machinery. This process is usually automated and allows for complex shapes to be produced with minimal tooling cost. The finished sections are then left to cure in a warm, ventilated area.
Recyclability
Today’s world would not function very well without glass fiber reinforced plastics. GRP is a composite material whose thermosetting polymer matrix is reinforced with finely woven glass fibres. It is a versatile product and it is often used to replace materials such as metal, concrete and wood in products where durability and corrosion resistance are important requirements.
The resin that is used to make GRP can vary, but it is usually based on an epoxy, vinyl ester or polyester thermosetting polymer. The fibres can be randomly arranged, or they may be flattened into a sheet called a chopped strand mat or woven into glass cloth.
The physical recycling of GFK with the use of mechanical methods has a number of suggestions to counteract downgrading such as adding longer fiber lengths to the recyclate. This method, however, is not suitable for continuous fibre-reinforced composites and is therefore restricted to short glass fiber-reinforced GFK. The recyclability of GRP is also affected by the type of glass that is used.